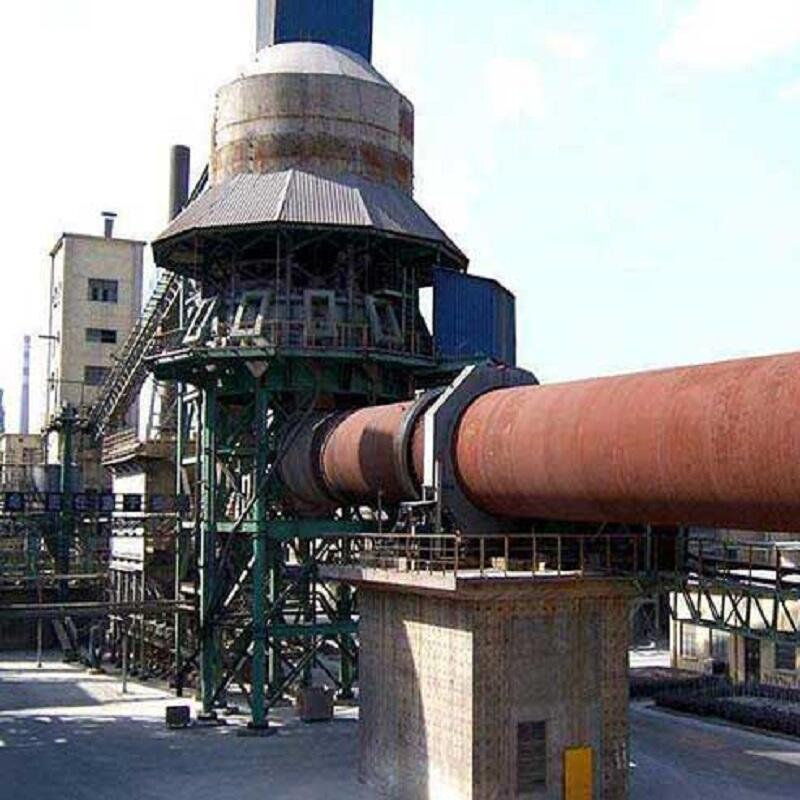
Çakıl taşının kalsinasyonu için karışık ateşle dönen kireç fırını
Kapasite: | 200-1200 t/g (ayarlanabilir) |
Kapurtaşısı Parçacık Boyutu: | 20-40mm |
Yakıt: | gaz, toz kömür, vb. |
Etkinlik Derecesi: | 360-400 ml |
Özellikler: | küçük besleme parçacık boyutu, yüksek fiyat, yüksek etkinlik değeri, çeşitli yakıtlar mevcut, yüksek otomasyon ve düşük ısı tüketimi. |
Genel Bakış
Sorgu
İlgili Ürünler
Tanım:
Çökelik döner fırın, aynı zamanda döner fırın olarak da bilinir ve yapı malzemeleri ekipmanı kategorisine giren bir hareketli kalsinasyon cihazıdır. Önemli avantajları arasında büyük üretim kapasitesi, sessiz çalışması ve düşük genel enerji tüketimi yer almaktadır. Çökelik üretimi için temel bir işleme aracı olan bu ekipman, önemli endüstriyel değere sahip olmasından dolayı yüksek talep gören bir üründür. Çökelik, inşaat, yapı malzemeleri, metalürji, kimya, hafif sanayi, çevresel koruma, tıp ve tarım gibi çeşitli alanlarda yaygın olarak kullanılmaktadır. Özellikle çelik imalatı, demir imalatı, sinterleme, bakır, alüminyum eritimi ve diğer endüstrilerde çökelik, slaglayıcı madde, çözücü veya sinterleme maddesi olarak önemli bir rol oynamaktadır. Bu geniş uygulama alanı, çökelik döner fırının çeşitli endüstriyel ortamlardaki esnekliği ve önemiyle öne çıkmaktadır.
Özellikler:
Çökelik döner fırınınin teknik özellikleri | ||||||||||||
Kapasite (t/g) | 150 | 200 | 250 | 300 | 350 | 400 | 500 | 600 | 750 | 800 | 1000 | |
Ürün | Etkin çökelik, kalsiné edilmiş dolomit | Etkin çökelik, kalsiné edilmiş dolomit | Etkin çökelik, kalsiné edilmiş dolomit | Etkin çökelik, kalsiné edilmiş dolomit | Etkin çökelik, kalsiné edilmiş dolomit | Etkin çökelik, kalsiné edilmiş dolomit | Etkin çökelik, kalsiné edilmiş dolomit | Etkin çökelik, kalsiné edilmiş dolomit | Etkin çökelik, kalsiné edilmiş dolomit | Etkin çökelik, kalsiné edilmiş dolomit | Etkin çökelik, kalsiné edilmiş dolomit | |
Önısıtma cihazı | Dairesel dikey önısıtma veya çokgenal dikey önısıtma | Dairesel dikey önısıtma veya çokgenal dikey önısıtma | Dairesel dikey önısıtma veya çokgenal dikey önısıtma | Dairesel dikey önısıtma veya çokgenal dikey önısıtma | Dairesel dikey önısıtma veya çokgenal dikey önısıtma | Dairesel dikey önısıtma veya çokgenal dikey önısıtma | Dairesel dikey önısıtma veya çokgenal dikey önısıtma | Dairesel dikey önısıtma veya çokgenal dikey önısıtma | çokgenal dikey önısıtma | çokgenal dikey önısıtma | çokgenal dikey önısıtma | |
Döner fırın | boyut(m) | φ2.5×40 | φ2.8×42 | φ3×46 | φ3.2×50 | φ3.5×54 | φ3.6×56 | φ3.8×58 | φ4×60/Φ4.2×50 | φ4.3×58 | φ4.3×64 | φ4.8×68 |
Etkin hacim (m³) | 142 | 190 | 235 | 292 | 390 | 430 | 505 | 575/548 | 670 | 738 | 1005 | |
Sıcaklık (°C) | 1350/1250 | 1350/1250 | 1350/1250 | 1350/1250 | 1350 | 1350 | 1350 | 1350 | 1350 | 1350 | 1350 | |
Soğutucu | Kare dikey soğutma cihazı | Kare dikey soğutma cihazı | Kare dikey soğutma cihazı | Kare dikey soğutma cihazı | Kare dikey soğutma cihazı | Kare dikey soğutma cihazı | Kare dikey soğutma cihazı | Kare dikey soğutma cihazı | Kare dikey soğutma cihazı | Kare dikey soğutma cihazı | Kare dikey soğutma cihazı | |
Yakıt | Gaz, toz kömür | Gaz, toz kömür | Gaz, toz kömür | Gaz, toz kömür | Gaz, toz kömür | Gaz, toz kömür | Gaz, toz kömür | Gaz, toz kömür | Gaz, toz kömür | Gaz, toz kömür | Gaz, toz kömür | |
Isı oranı (KJ/KgC3O) | 5300/5000 | 5300/5000 | 5300/5000 | 5300/5000 | 5225 | 5225 | 5100 | 5100 | 4810 | 4810 | 4810 |
Çalışma prensibi:
Kiln'un sonunda bulunan kanal vasıtasıyla kireçtaşı kiln'a sokulur. Kiln gövdesinin eğimi ve yavaş dönmeleri kullanılarak, kireçtaşı bir yanda çevresel olarak ilerler ve diğer tarafta eksen boyunca kiln'un sonundan başlayarak kiln başına doğru hareket eder. Yakıt, kiln'un sonundaki yakıcı vasıtasıyla içeriye girer, yanma işlemine tabi tutulur ve üretilen ısı, radyasyon, konveksiyon ve iletme yoluyla kireçtaşına aktarılır. Kireçtaşı bu hareket esnasında kalsinasyon geçirir ve sodyum kireciye dönüşür, ardından kiln'un sonundan dışarı atılır. Aynı anda, yüksek sıcaklıklı tün şesi kiln'un sonundan toz kaldırma sistemine yönlendirilir.
Rekabet Avantajı:
l Yenilikçi Teknoloji: Ana sürüş sistemi şimdi gelişmiş AC frekans dönüşümü hız düzenleyici teknolojisini kullanmaktadır. Bu teknoloji, geleneksel manyetik ve DC hız düzenleyicilerine kıyasla, enerji verimliliği, çevresel uyumluluk, geniş hız düzenleme aralığı, yüksek hız düzenleme hassasiyeti ve istikrarlı çalışmayı sağlar.
kurulumdaki Hassasiyet ve Güvenilirlik: Destek tekerleği ve tutan tekerleğin destek cihaz tabanının kaynaklandığı ve titreşim yaşaması ile kaynaklanma gerilmelerinin ortadan kaldırıldığından, büyük dikey torno ve deliş ve freze makineleri ile entegre işleme yapılması, her bir parçanın işlemsel doğruluğunu, şekli ve konum toleransını garanti altına alır. Bu yaklaşım, tüm sistemin kurulum doğruluğunu ve güvenilirliğini önemli ölçüde artırır.
l Sürüklü İşlem: Geleneksel döner fırınlarda görülen fırın kuyruğundaki geri dönüş malzemesi ve yaygın toz sızıntı sorunlarını ele almak için, fırının başı ve son kısmı genel yapısal iyileştirmeye tabi tutuldu. Bu tasarım, kireçtaşı'nın ve onun yakma süreci gereksinimlerine uygun daha süreklı ve doğal bir madde taşıma sağlar.
l Sabit Kalite: Kireçtaşı eşit şekilde ısıtılır ve bu da ürün kalitesinin sabit olmasını ve düşük aşırı yanma oranını sağlar. Bu, çelik imalatı için yüksek aktiviteye sahip kireçin yakılması için özellikle uygundur.
l Esnek Süreç Yapılandırması: Fırının sonuna dikey önısıtıcı eklenmesi, kireç döner fırınından gelen yüksek sıcaklıklı tün tüplerin tamamen kullanılmasını sağlar. Bu, kireçtaşını çevresel sıcaktan başlangıç ayrışımı durumuna kadar önısıtırır, ürün aktivitesini artırır ve taşıma ve depolamayı kolaylaştırır.